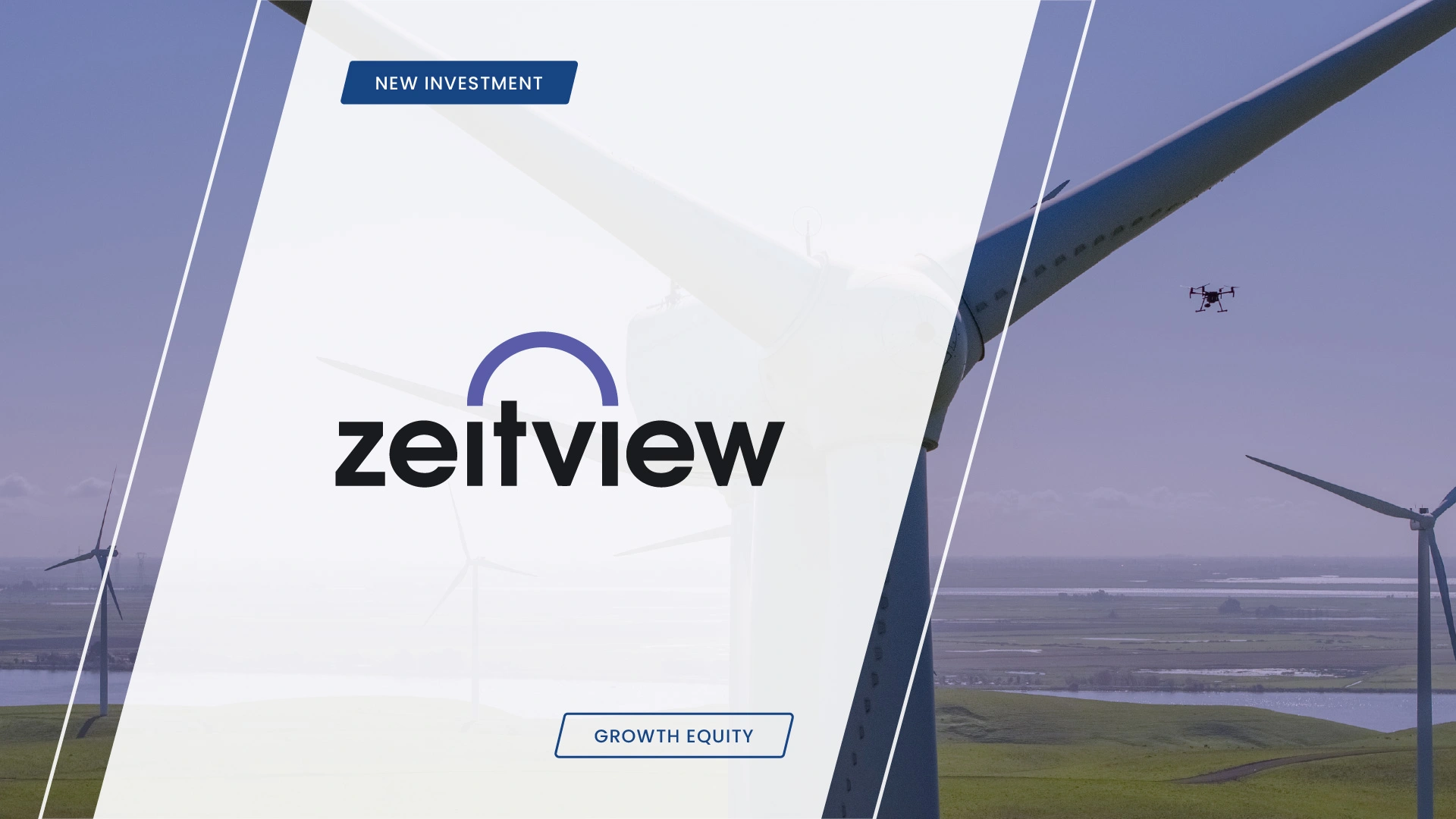

As industries globally race to reduce their emissions, carbon capture has emerged as one of the defining technological solutions of the century. While most people envision captured CO₂ being stored underground or in geological formations, what if, instead, carbon emissions could be harnessed as a resource to reduce more carbon at a scale commensurate with our global emissions challenge?
Turning waste carbon dioxide and industrial byproducts from an environmental liability into the next generation of circular materials may sound too good to be true, but Calgary-based Carbon Upcycling Technologies is doing it now to decarbonize the literal foundation of modern infrastructure – cement and concrete.
Carbon Upcycling Technologies (CUT) has pioneered an end-to-end decarbonization technology that captures and utilizes CO2 emissions upcycle industrial waste and CO2 into enhanced Supplementary Cementitious Material (SCM). This replaces clinker in cement production, reducing carbon emissions by up to 60% while improving the strength and durability of concrete.
Headquarters: Calgary, Canada; Globally applicable, currently focused on industries including cement and concrete and Advanced Materials (AdMs).
Concrete overview:
Advanced Materials Overview
Leadership:
Apoorv Sinha
Website:
carbonupcycling.com
Contact person:
Madison Savilow
“Hard-to-abate industries like cement, steel, mining and chemicals account for nearly 25% of all global CO2 emissions,” explains Carbon Upcycling’s CEO Apoorv Sinha.
“This share of the pie will only continue to increase as global populations swell. We can help these industries decarbonize together by enabling a circular pathway for their carbon emissions and solid waste byproducts to be upcycled into tomorrow’s CO2-embedded, high-performance materials.”
Carbon Upcycling’s commercial technology taps into the millions of tonnes of solid waste byproducts in existence today to sequester point-source CO2 emissions and produce up to 60% lower carbon cement compared to conventional cement. It works by accelerating the natural process of carbon mineralization from what takes nature hundreds of years to achieve, takes Carbon Upcycling a few hours.
This innovative process democratizes carbon capture and storage, removing its limitations to select regions by turning concrete infrastructure into a carbon sink, without excessive use of water or strain on the electric grid. Most importantly, this technology enables stronger, more climate-resilient concrete at cost-parity with today’s cement prices.
The benefit of Carbon Upcycling’s technology was evidenced by the results of a recent three-year study conducted by the Minnesota Department of Transportation (MnDOT) and the National Road Research Alliance (NRRA) to test new low-carbon concrete mixes. Running from 2021 to early 2024, MnDOT and NRRA compared 16 concrete mixes with the aim of identifying technologies capable of reducing the embodied carbon content of concrete paving, while maintaining or improving performance.
Carbon Upcycling partnered with Burnco, a North American leader in building materials, to deploy 140 m3 of active concrete highway for the study. The innovative mixture was composed of 10% limestone and 30% reclaimed fly ash enhanced by Carbon Upcycling’s carbon capture and utilization process, and was compared to an untreated control mix alongside 14 other mix designs.
Independent verification of the study showed the mixture from Carbon Upcycling and Burnco was 28% stronger at 28 days and 32% more resistive to chloride at 56 days, and had 12.5% less total cementitious material than the control mix.
Reducing cementitious content results in substantial material, carbon, and cost savings. Researchers also found no notable difference in the workability of Carbon Upcycling’s mix compared to traditional concrete, demonstrating the product’s success at every stage of value chain.
Carbon Upcycling submitted a “very impressive mixture design” to the trial reflects Larry Sutter, MnDOT’s Principal Engineer on the project, “it accomplished the highest reduction in total cementitious materials of all mixture designs submitted.”
Sinha adds, “The project with MnDOT demonstrated that we have a readily deployable, drop-in solution to decarbonize cement that performs how teams on the ground expect – reducing embodied carbon while meeting or exceeding performance standards without the price premium.”
Carbon Upcycling’s innovative technology has caught the attention of cement supermajors around the world with the likes of Cemex, CRH, and Titan investing in the company to unlock low-carbon cement production for their own facilities. Since 2021, Carbon Upcycling has operated a commercial demonstration facility co-located at a natural gas power plant and deployed over 3,000 tonnes of low-carbon cement across the local built environment.
Now, it’s breaking ground on its first-of-a-kind commercial facility co-located at one of Canada’s largest cement plants. The project with Ash Grove Cement, a CRH company, will upcycle CO2 emissions from the cement kiln and steel slag sourced locally into a low-carbon blended cement. Carbon Upcycling and CRH’s collaboration aligns with both companies’ commitment to localizing supply chains and creating a circular, low-carbon future.
Carbon Upcycling’s team has successfully demonstrated the technology working with a wide range of feedstocks; including industrial byproducts like reclaimed ash, steel slags, and clays.
Using industrial byproducts in cement is not new, but as industries electrify and coal is phased out, the dwindling availability of high-quality domestic materials can be a challenge for cement producers to find usable materials locally. Carbon Upcycling’s technology addresses this challenge head on.
“In certain families of materials, we are able to directly capture CO2 from on-site flue stacks as is, and work with a range of carbon concentrations – from as little as 3%, right up to 99% (by volume). By using locally available materials and sequestering CO2 at the source, we’re removing the need for additional infrastructure and energy, helping keep costs low”.
Carbon Upcycling’s success is growing rapidly. High profile awards have seen the company named in the internationally recognized World Economic Forum’s Tech Pioneers list for 2024, one of only 100 chosen from around the world each year, and as a Reuters Top 100 innovator Leading the Energy Transition.